In
recent weeks, a few of our board game fan
a
tics have met on Friday evenings in Tog. We have played some games, we laughed & decided to utilize laser cutter to make extra sturdy Acrylic tokens for a game called Androind: Netrunner. A good bit of graphical artwork was already online (thx for a great design) and after some manipulation it was ready to be cut. Other designs had to be done from scratch. So far we have designed & prototype cut all the regular size tokens. There is a plan to cut large size Credits Sets as well.
Android: Netrunner is an asymmetrical Living Card Game for two players. Set in the cyberpunk future of Android and Infiltration, the game pits a megacorporation and its massive resources against the subversive talents of lone runners.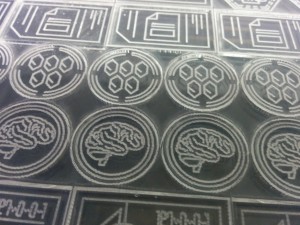
Corporations seek to score agendas by advancing them. Doing so takes time and credits. To buy the time and earn the credits they need, they must secure their servers and data forts with “ice”. These security programs come in different varieties, from simple barriers, to code gates and aggressive sentries. They serve as the corporation’s virtual eyes, ears, and machine guns on the sprawling information superhighways of the network.
In turn, run
ners need to spend their time and credits acquiring a sufficient wealth of resources, purchasing the necessary hardware, and developing suitably powerful ice-breaker programs to hack past corpo
rate security measures. Their jobs are always a little desperate, driven by tight timelines, and shrouded in mystery. When a runner jacks-in and starts a run at a corporate server, he risks having his best programs trashed or being caught by a trace program and left vulnerable to corporate countermeasures. It’s not uncommon for an unprepared runner to fail to bypass a nasty sentry and suffer massive brain damage as a result. Even if a runner gets through a data fort’s defenses, there’s no telling what it holds. Sometimes, the runner finds something of value. Sometimes, the best he can do is work to trash whatever the corporation was developing.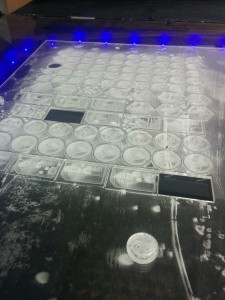
The first player to seven points wins the game, but likely not before he suffers some brain damage or bad publicity!
More about the game: https://www.fantasyflightgames.com/en/products/android-netrunner-the-ca
rd-game/
Would you like to try to laser cut your own designs? Come along to our ongoing (every second Monday) CAD workshop in Tog. Looking forward to see you here – 6th of July 2015.